En 2025, malgré les avancées technologiques qui nous promettent monts et merveilles (intelligence artificielle, maintenance prédictive, automatisation...), de nombreuses usines continuent de tourner en sous-régime.
Pourtant, le potentiel est bien là. Les sites industriels les plus performants l'ont compris : la différence entre une production qui ronronne et une qui tousse ne tient parfois qu'à quelques erreurs. Des erreurs classiques, certes, mais qui plombent directement votre TRS et votre compétitivité.
Dans ce guide, nous avons identifié les erreurs les plus critiques qui freinent encore la performance de votre production. Pour chacune d'entre elles, vous découvrirez :
- Pourquoi vous les commettez (peut-être) sans le savoir
- Ce qu'elles coûtent réellement à votre production
- Comment les corriger, simplement et efficacement
Alors, prêt à améliorer votre suivi de production ?
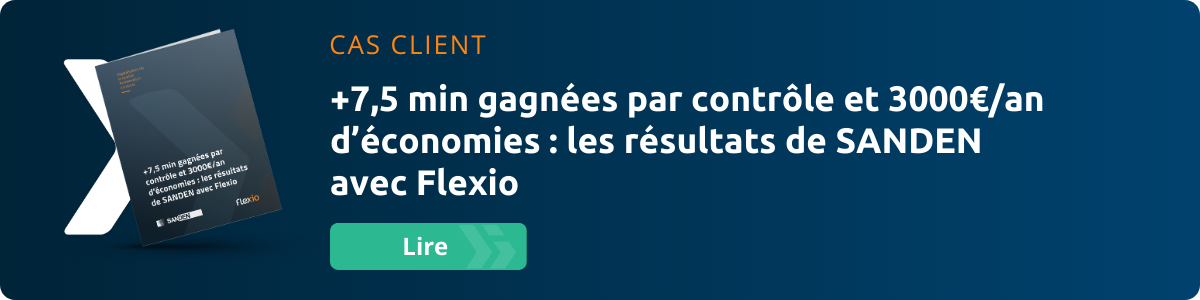
Erreur n°1 : Passer à côté des données essentielles de production
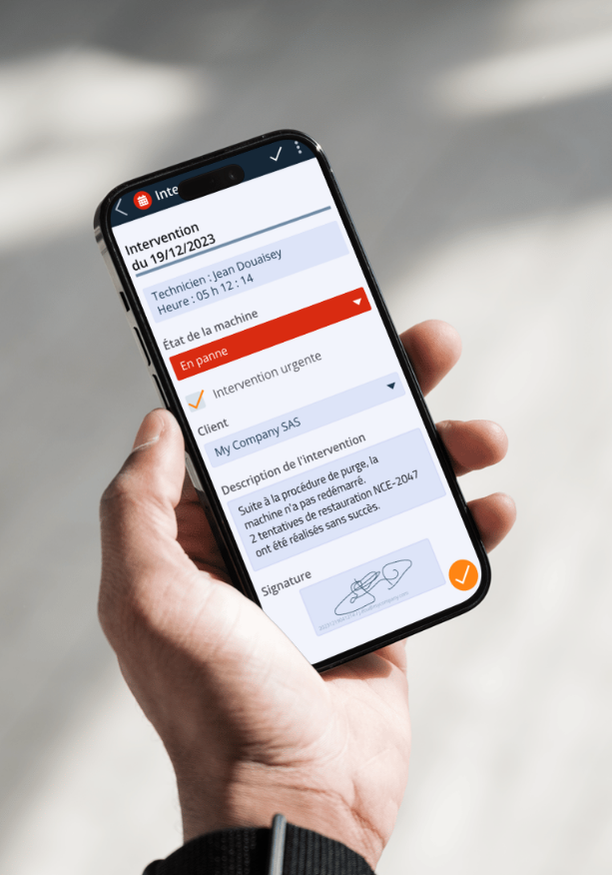
Imaginez-vous aux commandes d'un avion avec un tableau de bord dont la moitié des voyants serait en panne. Rassurant, non ? C'est pourtant la réalité de nombreuses usines qui fonctionnent sans visibilité, faute d'avoir accès aux bonnes données au bon moment.
Pourquoi on tombe dans le piège ?
- Le classique : "On a toujours fait comme ça"
- Les feuilles papier qui s'accumulent dans un coin : "Les opérateurs notent tout sur leurs cahiers"
- La peur du changement (et de la résistance au changement)
Les conséquences :
- Des décisions prises au feeling plutôt que sur des faits
- Des problèmes détectés trop tard (quand la machine est déjà en panne...)
- Des pertes de productivité invisibles mais bien réelles
- Une maintenance qui joue aux pompiers plutôt qu'à la prévention
Comment s'en sortir ?
Étape 1 : identifiez vos données critiques
Pour initier votre transformation, commencez par cartographier les données essentielles à votre performance. Concentrez-vous d'abord sur les indicateurs qui impactent directement votre TRS. Puis analysez vos process pour identifier les points de contrôle stratégiques et les données manquantes qui vous empêchent d'anticiper les problèmes.
Étape 2 : moderniser la collecte, automatisez-là
Il est temps de moderniser votre collecte de données : abandonnez progressivement les relevés manuels, sources d'erreurs et chronophages, au profit de systèmes digitaux. Déployez par exemple des capteurs connectés aux points stratégiques et mettez en place des formulaires numériques accessibles sur tablette ou mobile pour centraliser toutes vos données. Cette automatisation vous permettra d'obtenir des informations fiables en temps réel.
Étape 3 : rendez les données accessibles
La dernière étape consiste à transformer ces données en informations actionnables. Développez des tableaux de bord personnalisés qui répondent aux besoins spécifiques de chaque service. Configurez des alertes pertinentes pour détecter rapidement les dérives. L'objectif est de rendre l'information claire, accessible et utile pour tous les acteurs de votre production.
Notre conseil : allez-y étape par étape et co-construisez ce changement avec vos équipes. Une fois que les premières actions auront été menées, testées et approuvées, vos équipes seront demandeuses pour digitaliser d'autres processus.
"Je pense que nous gagnons minimum 5hpar semaine ! Ceci grâce à une gestion centralisée et unemise en priorité nous permettant denous concentrer sur l’essentiel et donc, de gagner en efficience globale." - Sebastien Perrin, Directeur des opérations - Wedo
Erreur n°2 : L'absence de standardisation des processus
Dans l'industrie 4.0, la standardisation n'est plus une option mais une nécessité. Pourtant, de nombreuses entreprises peinent encore à mettre en place des processus standardisés efficaces, limitant ainsi leur potentiel de performance.
Pourquoi on tombe dans le piège ?
- La résistance au changement dans les équipes (encore elle !)
- Le manque de temps et de ressources pour formaliser les processus
- La complexité des opérations qui semblent trop spécifiques
- La crainte de perdre en flexibilité opérationnelle
- Le cloisonnement entre les services qui maintient des pratiques disparates
Les conséquences
- Une qualité inconstante des produits
- Des erreurs récurrentes qui auraient pu être évitées
- Une formation complexe des nouveaux collaborateurs
- Une difficulté à identifier les sources réelles des problèmes
- Une perte de temps et d'efficacité dans les opérations quotidiennes
Comment mettre de l'ordre dans tout ça ?
Étape 1 : cartographiez vos processus
Commencez par identifier vos processus critiques, ceux qui ont le plus d'impact sur votre performance. Documentez les différentes méthodes existantes au sein de vos équipes (avec vos équipes !). Cette phase d'observation vous permettra de repérer les meilleures pratiques déjà en place et de comprendre les variations entre les équipes ou les shifts.
Étape 2 : standardisez intelligemment
Élaborez des procédures claires et visuelles et impliquez directement vos opérateurs dans cette démarche : ce sont eux qui connaissent le mieux le terrain et qui devront appliquer ces standards au quotidien. Profitez-en pour digitaliser ce qui ne l'est pas, en créant vous-mêmes des applications. Notre conseil : n'oubliez pas d'intégrer une certaine flexibilité pour gérer les cas exceptionnels - un standard trop rigide risque d'être contourné.
Avec Flexio, vous créez vos formulaires, les reliez à votre base et configurez des tableaux de bords et scénarios d'automatisation (ex : alertes, reporting) en quelques jours.
Étape 3 : faites vivre vos standards
Mettez en place un programme de formation structuré pour assurer une adoption uniforme des nouveaux standards. Instaurez des routines de contrôle pour mesurer leur application et leur efficacité. Surtout, créez un système de feedback permettant aux équipes de proposer des améliorations. Les standards doivent évoluer avec votre organisation et intégrer les retours du terrain pour rester pertinents.
Erreur n°3 : Privilégier la maintenance réactive plutôt que préventive
"Dans l’industrie automobile, chaque arrêt coûte environ 1,3 M$ par heure, ce qui correspond au temps de production perdu et, par conséquent, aux ventes perdues. Malgré l’impact significatif des temps d’arrêt, 70 % des entreprises n’ont toujours pas de visibilité sur le moment où leurs équipements devraient être arrêtés et où il faudrait intervenir afin d’éviter les arrêts non planifiés. Seules 26% ont adopté une stratégie de maintenance prédictive, basée sur des données et des algorithmes qui permettent d’identifier avec plus de précision les moments optimaux pour la maintenance des équipements."
Pourquoi on tombe dans le piège ?
- Le budget limité pour investir dans des outils de maintenance préventive
- Le manque de personnel qualifié pour mettre en place une stratégie préventive
- La pression de production qui pousse à reporter les interventions
- La difficulté à justifier des arrêts planifiés face à la direction
- L'absence d'historique fiable des pannes et interventions
Les conséquences concrètes
- Des arrêts de production non planifiés et coûteux
- Des réparations d'urgence 3 à 4 fois plus chères
- Une usure accélérée des équipements
- Des pertes de production importantes
- Une désorganisation des équipes de maintenance
Comment passer en mode préventif ?
Étape 1 : établissez une stratégie claire
La transition vers une maintenance préventive commence par une stratégie bien définie. Commencez par réaliser un audit complet de votre parc machines pour identifier vos équipements critiques - ceux dont la panne aurait le plus d'impact sur votre production. Définissez ensuite des indicateurs de performance clés comme le MTBF (Temps Moyen Entre Pannes) et le MTTR (Temps Moyen de Réparation). Ces données vous permettront de construire un planning d'interventions préventives basé sur des faits plutôt que sur des suppositions. L'objectif est de passer d'une approche réactive à une approche planifiée et maîtrisée.
Étape 2 : déployez les bons outils
La maintenance préventive moderne s'appuie sur des outils technologiques adaptés. Investissez dans des capteurs de surveillance (IoT) pour suivre en temps réel les paramètres critiques de vos équipements (température, vibrations, consommation électrique...). Implémentez une GMAO (Gestion de Maintenance Assistée par Ordinateur) performante qui centralisera toutes vos données de maintenance et vous aidera à planifier vos interventions. Créez des tableaux de bord qui permettront à vos équipes de visualiser facilement l'état de santé des équipements et les interventions à venir. Vous pouvez faire tout cela avec Flexio !
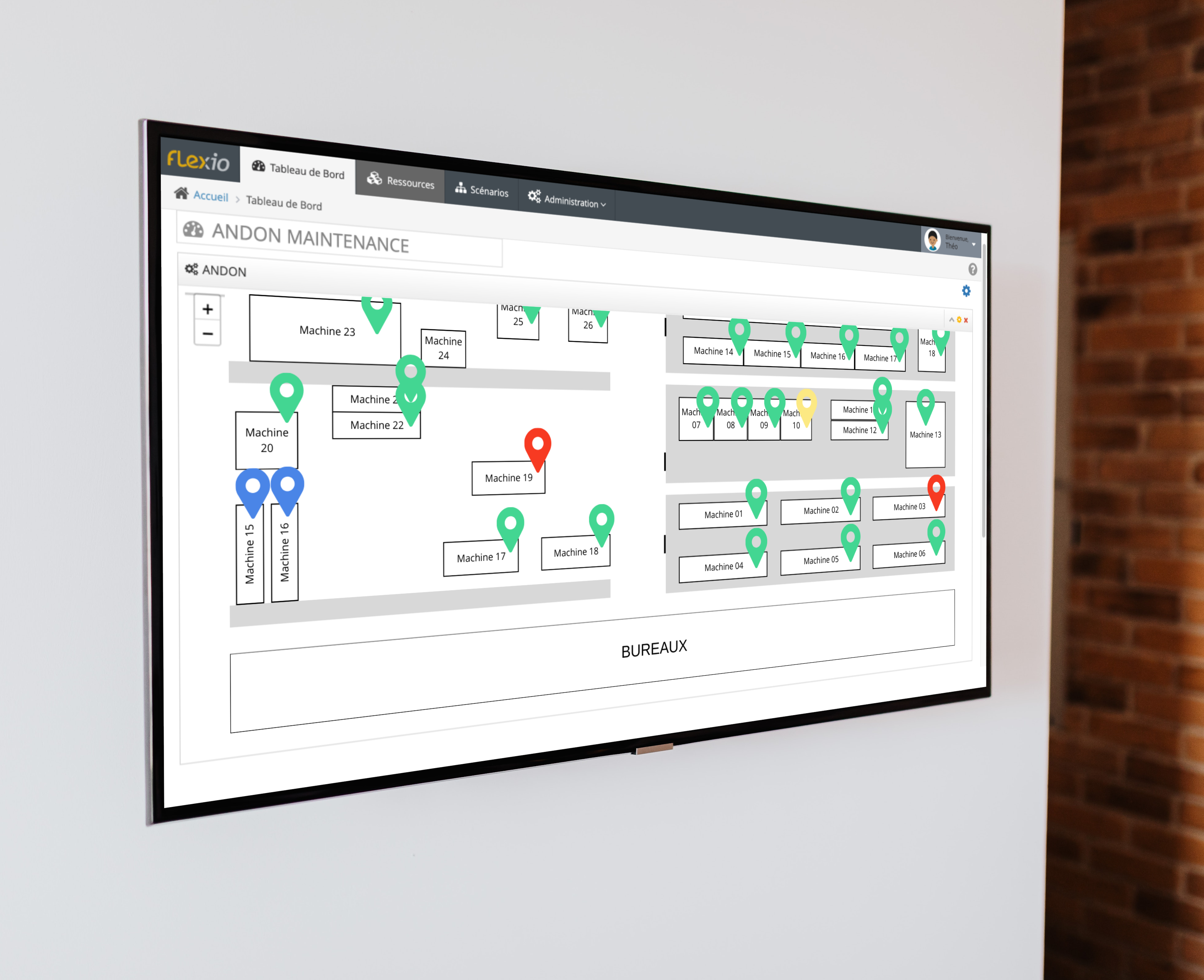
Étape 3 : formez vos équipes
La technologie seule ne suffit pas - vos équipes sont la clé du succès. Développez les compétences de vos techniciens, formez-les aux nouvelles technologies de maintenance prédictive. Plus important encore, travaillez sur le changement de culture : passez d'une mentalité de "pompier" à celle de "préventeur". Valorisez les actions préventives et la détection précoce des anomalies plutôt que les interventions d'urgence.
Erreur n°4 : Le manque de communication inter-services
La majorité des dirigeants identifient la communication inefficace entre départements comme cause principale d'échec, et pourtant, de nombreuses usines continuent de fonctionner en silos. Un frein majeur à la performance industrielle.
Pourquoi on tombe dans le piège ?
- L'organisation hiérarchique traditionnelle qui favorise les silos
- Les objectifs différents entre services qui créent des tensions
- Les outils de communication non adaptés ou mal utilisés
- Le manque de temps pour organiser des réunions inter-services
- L'absence de processus formalisés de partage d'information
Les conséquences concrètes
- Des retards de production dus aux informations non partagées
- Des décisions prises sans vision globale
- Des problèmes qualité qui se répètent
- Une perte de temps en résolution de conflits
- Une démotivation des équipes
Comment améliorer la communication ?
Étape 1 : Structurez les échanges
La première étape consiste à mettre en place une structure de communication claire et efficace. Instaurez des réunions quotidiennes courtes (10-15 minutes maximum) au début de chaque shift, où chaque responsable de chaque service partage les objectifs du jour, ses contraintes, les problèmes rencontrés la veille, points de vigilance, etc.
Étape 2 : Déployez les bons outils
Une communication efficace nécessite des outils adaptés. Mettez en place une plateforme centralisée où toutes les informations importantes sont accessibles en temps réel : indicateurs de production, planning de maintenance, objectifs qualité, etc. L'outil idéal doit être simple d'utilisation, accessible sur différents supports (PC, tablettes, smartphones) et permettre une traçabilité des échanges (on ne peut que vous recommander notre outil Flexio !). Évitez la multiplication des canaux de communication qui créent de la confusion et de la perte d'information.
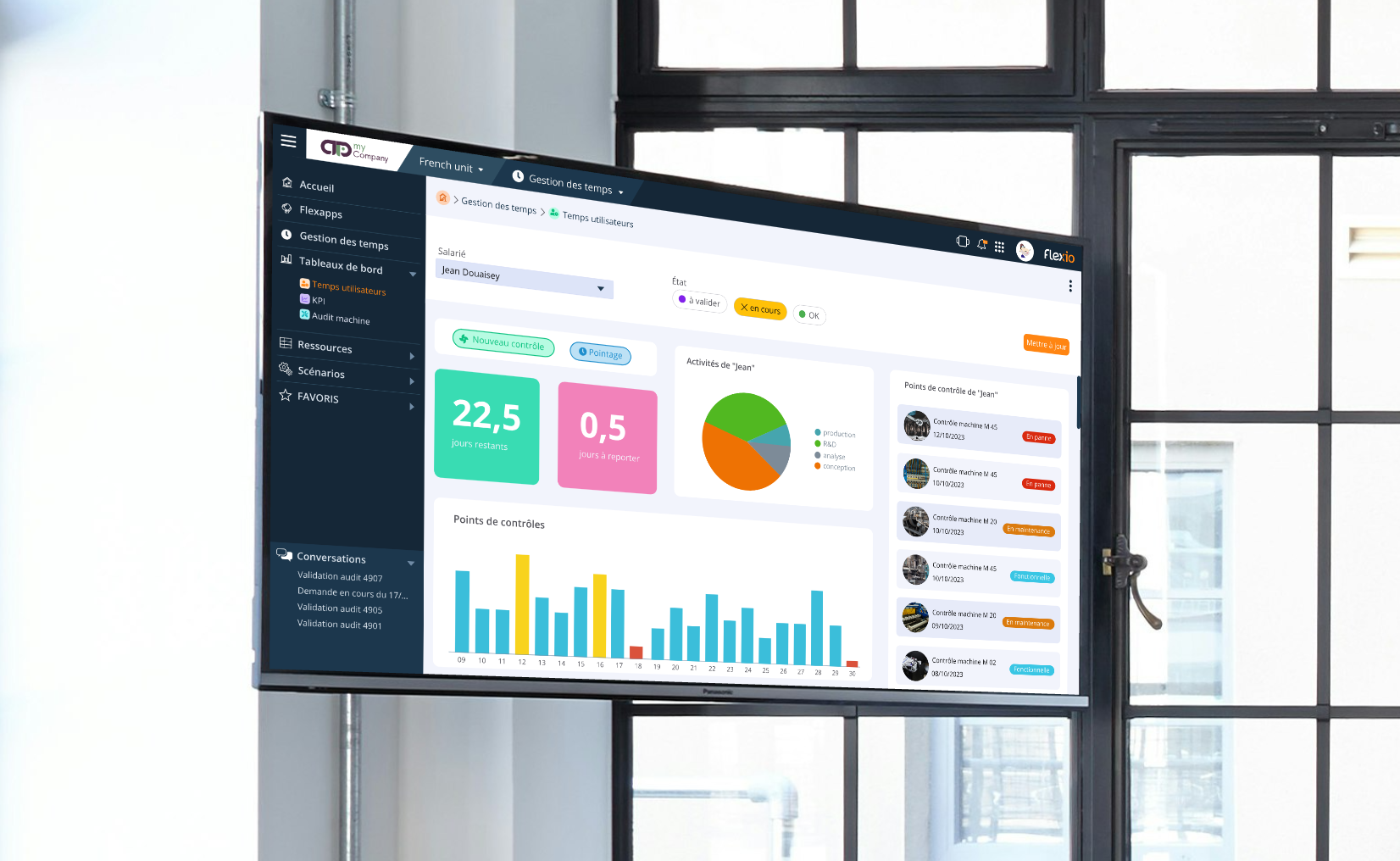
Étape 3 : Développez une culture collaborative
La technologie ne peut pas tout - la culture d'entreprise est essentielle. Formez vos managers à la communication transverse et à l'animation d'équipes multi-services. Instaurez des mécanismes de reconnaissance qui valorisent les succès collectifs plutôt que les performances individuelles. Créez des espaces et des moments dédiés au partage de bonnes pratiques entre services.
Erreur n°5 : Le manque de visibilité sur les temps d'arrêt machine
Le TRS (Taux de Rendement Synthétique) est l'indicateur clé de la performance industrielle, cependant, de nombreuses entreprises naviguent encore à l'aveugle et réduisent difficilement leurs temps d'arrêt machine.
Pourquoi on tombe dans le piège ?
- La collecte manuelle des données qui génère des imprécisions
- L'absence d'outils de suivi en temps réel
- La difficulté à catégoriser correctement les types d'arrêts
- Le manque de formation des opérateurs sur l'importance du suivi
- La multiplication des micro-arrêts difficiles à tracer
Les conséquences concrètes
- Un TRS sous-évalué ou mal calculé
- Des pertes de production non identifiées
- Une maintenance mal planifiée
- Des décisions basées sur des données incomplètes
- Une impossibilité d'optimiser réellement la production
Comment gagner en visibilité ?
Étape 1 : structurez votre suivi
La première étape vers une meilleure visibilité est la mise en place d'une structure de suivi rigoureuse. Commencez par établir une classification claire et précise de vos temps d'arrêt. Distinguez les arrêts propres (liés directement à la machine : pannes, réglages, changements d'outils) des arrêts induits (externes : manque de matière, absence d'opérateur, problèmes qualité). Définissez des indicateurs pertinents pour chaque catégorie : durée moyenne des arrêts, fréquence, impact sur la production.
Étape 2 : automatisez la collecte
Une fois votre structure définie, modernisez votre système de collecte de données. Comme déjà expliqué à l'erreur n°1 : l'ère du papier et du crayon est révolue. Déployez des capteurs connectés sur vos équipements critiques pour suivre automatiquement les temps d'arrêt. Implémentez un logiciel tel qu'un système MES (Manufacturing Execution System) ou/et un logiciel no-code comme Flexio, qui centralise toutes ces données en temps réel. Configurez des tableaux de bord dynamiques qui permettent de visualiser instantanément l'état de vos machines et l'historique des arrêts.
Étape 3 : analysez pour progresser
La collecte de données n'est qu'un début - c'est leur analyse qui crée de la valeur. Mettez en place une routine d'analyse systématique de vos temps d'arrêt. Utilisez des outils d'analyse statistique pour identifier les causes racines des arrêts récurrents. Quantifiez l'impact financier de chaque type d'arrêt pour prioriser vos actions d'amélioration.
Erreur n°6 : Utiliser des outils rigides et inadaptés
Alors que la transformation numérique permet des gains de productivité considérables, de nombreuses entreprises restent prisonnières d'outils obsolètes ou inadaptés qui freinent leur développement.
Pourquoi on tombe dans le piège ?
- La peur du changement et de la perturbation des processus existants
- Les investissements passés dans des systèmes propriétaires
- La complexité perçue des nouvelles solutions
- Le manque de vision globale sur les besoins réels
- La difficulté à évaluer le ROI des nouveaux outils
Les conséquences concrètes
- Une perte de temps en manipulations manuelles ou développement spécifiques
- Une impossibilité d'adapter rapidement les process
- Des données dispersées et peu exploitables
- Une réactivité limitée face aux aléas
- Une démotivation des équipes face à des outils frustrants
Comment moderniser ses outils ?
Étape 1 : Évaluez vos besoins réels
Commencez par identifier les points de friction dans vos processus actuels : où perdez-vous du temps ? Quelles sont les tâches répétitives qui pourraient être automatisées ? Quelles données vous manquent pour prendre les bonnes décisions ? Impliquez les utilisateurs finaux dans cette phase d'analyse - ce sont eux qui connaissent le mieux les limites des outils actuels et les besoins réels du terrain.
Étape 2 : Choisissez des solutions flexibles
Le choix de vos nouveaux outils est déterminant pour l'avenir. Privilégiez des plateformes ouvertes qui peuvent communiquer facilement avec vos systèmes existants et futurs. Optez pour des solutions personnalisables qui pourront évoluer avec vos besoins, sans nécessiter de lourds développements informatiques. Évitez les solutions propriétaires trop rigides qui vous enferment dans un écosystème fermé et coûteux à maintenir.
Étape 3 : Accompagnez le changement
Commencez par des projets pilotes sur des périmètres restreints pour valider les choix techniques et affiner le déploiement. Identifiez des ambassadeurs dans chaque service qui pourront former et accompagner leurs collègues. Mesurez régulièrement les gains obtenus et communiquez-les largement pour maintenir la dynamique de changement.
La digitalisation : le levier incontournable de la performance industrielle
En 2025, la transformation numérique n'est plus une option : 82% des industriels estiment que leur entreprise ne survivra pas plus de 3 ans sans un engagement technologique fort. Mais comment réussir cette transformation ?
Les bénéfices concrets de la digitalisation
Optimisation des processus
- Réduction des erreurs humaines
- Automatisation des tâches répétitives
- Gain de temps sur les opérations quotidiennes
Amélioration de la visibilité
- Données en temps réel
- Tableaux de bord personnalisés
- Prise de décision facilitée
Augmentation de la réactivité
- Détection précoce des anomalies
- Maintenance prédictive
- Adaptation rapide aux changements
Les clés d'une digitalisation réussie
La transformation numérique doit être :
- Progressive pour faciliter l'adoption
- Adaptée aux besoins spécifiques
- Portée par les équipes terrain
- Créatrice de valeur mesurable
La solution Flexio : la digitalisation accessible
Flexio répond aux défis de la transformation numérique avec une approche unique :
Une plateforme no-code
- Création d'applications métier sans programmation (pas besoin d'être développeur !)
- Personnalisation selon vos besoins
- Déploiement rapide et évolutif
Des fonctionnalités qui s'adaptent à vos enjeux
- Formulaires
- Scénarios d'automatisation
- Disponibilité de vos applications sur mobile et tablette
- Tableaux de bord
- Connexion aux machines et systèmes d'informations
- Reporting
Une méthode progressive
- Digitalisation étape par étape
- Implication des équipes opérationnelles
- Accompagnement sur mesure
Des résultats concrets
Gains de productivité immédiats :
"Je fais en une journée ce que je fais sur Excel en une semaine" - Stephane Dupin, Responsable amélioration continue - STREIT
Une meilleure visibilité, pour une meilleur réactivité :
"Les tableaux de bord Flexio nous donnent une visibilité qu’on n’avait pas avant. on a gagné en réactivité sur nos contrôles qualité. En cas de dérive, on est alerté immédiatement par email avec toutes les infos clés (point de contrôle, valeur, photos...). On peut ainsi analyser et agir très vite, avant qu’il ne soit trop tard. C’est un vrai plus pour notre performance !." - Fabien Tanguy, Ingénieur Génie Industrie - SANDEN
Des équipes motivées et responsabilisées :
"Les bénéfices sont vite là : des processus fluidifiés, des équipes responsabilisées et des décisions facilitées. De quoi booster votre performance durablement !" - Jordan Thurnher, Responsable Lean Manufacturing - Cryostar
Mais aussi : réduction des non-conformités, amélioration de la traçabilité, satisfaction client accrue...
La digitalisation n'est plus réservée aux grands groupes. Avec Flexio, chaque industriel peut transformer ses défis en opportunités, en impliquant ses équipes dans la création de leurs propres outils.
À retenir : La digitalisation est un voyage, pas une destination. L'important est de commencer maintenant, avec les bons outils et le bon accompagnement.
.png)
Passez à l'action !
Nous avons identifié les erreurs majeures qui freinent la performance industrielle. La bonne nouvelle ? Chacune de ces erreurs représente une opportunité d'amélioration. En 2025, les solutions existent et sont plus accessibles que jamais.
La clé du succès : avancer pas à pas, en privilégiant des solutions flexibles qui s'adaptent à vos besoins spécifiques. La transformation numérique n'est pas une révolution, c'est une évolution progressive qui doit être portée par vos équipes.
Vous souhaitez aller plus loin ? Nos experts sont là pour vous accompagner dans l'analyse de vos processus et la mise en place de solutions adaptées. Contactez-nous pour un diagnostic personnalisé de votre situation.