Dans un contexte industriel marqué par une concurrence internationale accrue et des exigences clients toujours plus élevées, l'amélioration continue est une nécessité. Si les méthodes traditionnelles comme le Lean et le Kaizen ont fait leurs preuves, la transformation numérique ouvre aujourd'hui de nouvelles perspectives pour optimiser les processus industriels.
Mais comment moderniser efficacement ses méthodes d'amélioration continue ? Comment tirer parti des technologies de l'industrie 4.0 pour accélérer les gains de performance ?
Dans cet article, nous explorerons :
- Les fondamentaux des méthodes d'amélioration continue en industrie
- L'apport des technologies 4.0 dans l'optimisation des processus
- Les étapes clés pour digitaliser votre démarche d'amélioration continue
- Des exemples concrets de gains réalisés par les industriels
.png)
1. Les fondamentaux des méthodes d'amélioration continue en industrie
L'amélioration continue, ou "kaizen" en japonais, est une approche méthodique visant à optimiser constamment la performance industrielle. Contrairement aux grands projets de transformation qui impliquent des changements radicaux, elle mise sur une progression régulière et maîtrisée, particulièrement adaptée aux enjeux industriels actuels.
1.1 Les principes clés de l'amélioration continue moderne
La démarche d'amélioration continue repose sur quatre piliers fondamentaux, aujourd'hui enrichis par les possibilités du digital :
- L'élimination systématique des gaspillages : identification et suppression des tâches sans valeur ajoutée grâce à des outils de collecte et d'analyse de données en temps réel
- L'implication des équipes terrain : responsabilisation des collaborateurs via des applications métier intuitives et collaboratives
- La standardisation des bonnes pratiques : capitalisation et partage facilités par les outils numériques
- La mesure objective des résultats : suivi précis des indicateurs de performance grâce aux tableaux de bord digitaux
1.2 Les principales méthodes d'amélioration continue en industrie
Le Lean Management
Définition : Méthode d'optimisation des processus industriels visant à maximiser la valeur pour le client en éliminant systématiquement les gaspillages.
Principes clés :
- Identifier la valeur client
- Cartographier les flux de valeur
- Créer un flux continu
- Produire en flux tiré
- Viser la perfection
Outils associés : 5S pour l'organisation des postes de travail, SMED pour la réduction des temps de changement, TPM pour la maintenance, management visuel pour le pilotage de la performance.
La roue de Deming (PDCA)
.png)
Définition : Méthode itérative d'amélioration continue structurée en quatre étapes cycliques, permettant de résoudre méthodiquement les problèmes industriels.
Principes clés :
- Plan (Planifier) : analyser la situation et planifier des actions
- Do (Faire) : mettre en œuvre les actions
- Check (Vérifier) : mesurer les résultats obtenus
- Act (Agir) : pérenniser les bonnes pratiques si les résultats sont bons, sinon corriger et recommencer un cycle
Outils associés : Diagramme d'Ishikawa, 5 Pourquoi (5 why), indicateurs de performance (KPI), plans d'actions standardisés.
La méthode Kaizen
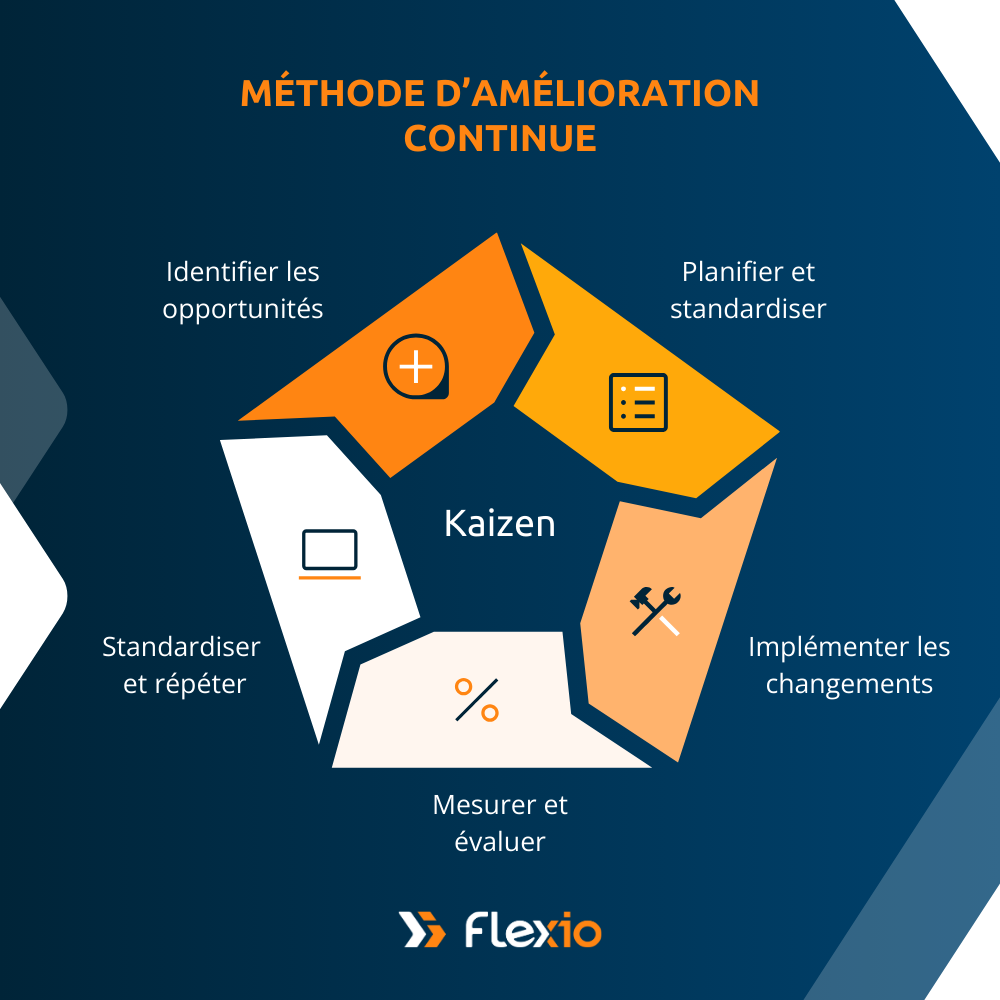
Définition : Approche japonaise d'amélioration continue basée sur des progrès constants et graduels, impliquant l'ensemble des collaborateurs.
Principes clés :
- Petites améliorations fréquentes
- Implication de tous les acteurs
- Focus sur le terrain
- Élimination des gaspillages
- Standardisation des bonnes pratiques
Outils associés : Ateliers Kaizen, cercles de qualité, système de suggestions, Gemba Walk (management terrain).
La méthode digitale et progressive Flexio
Définition : Approche moderne d'amélioration continue combinant méthodologies traditionnelles et outils digitaux pour optimiser les processus industriels.
Principes clés :
- Co-construction avec les équipes terrain
- Digitalisation progressive des processus
- Mesure en temps réel des performances
- Adaptation continue aux besoins métiers
Outils associés : Applications métier sur-mesure, formulaires numériques, automatisation des flux, tableaux de bord digitaux, management visuel connecté.
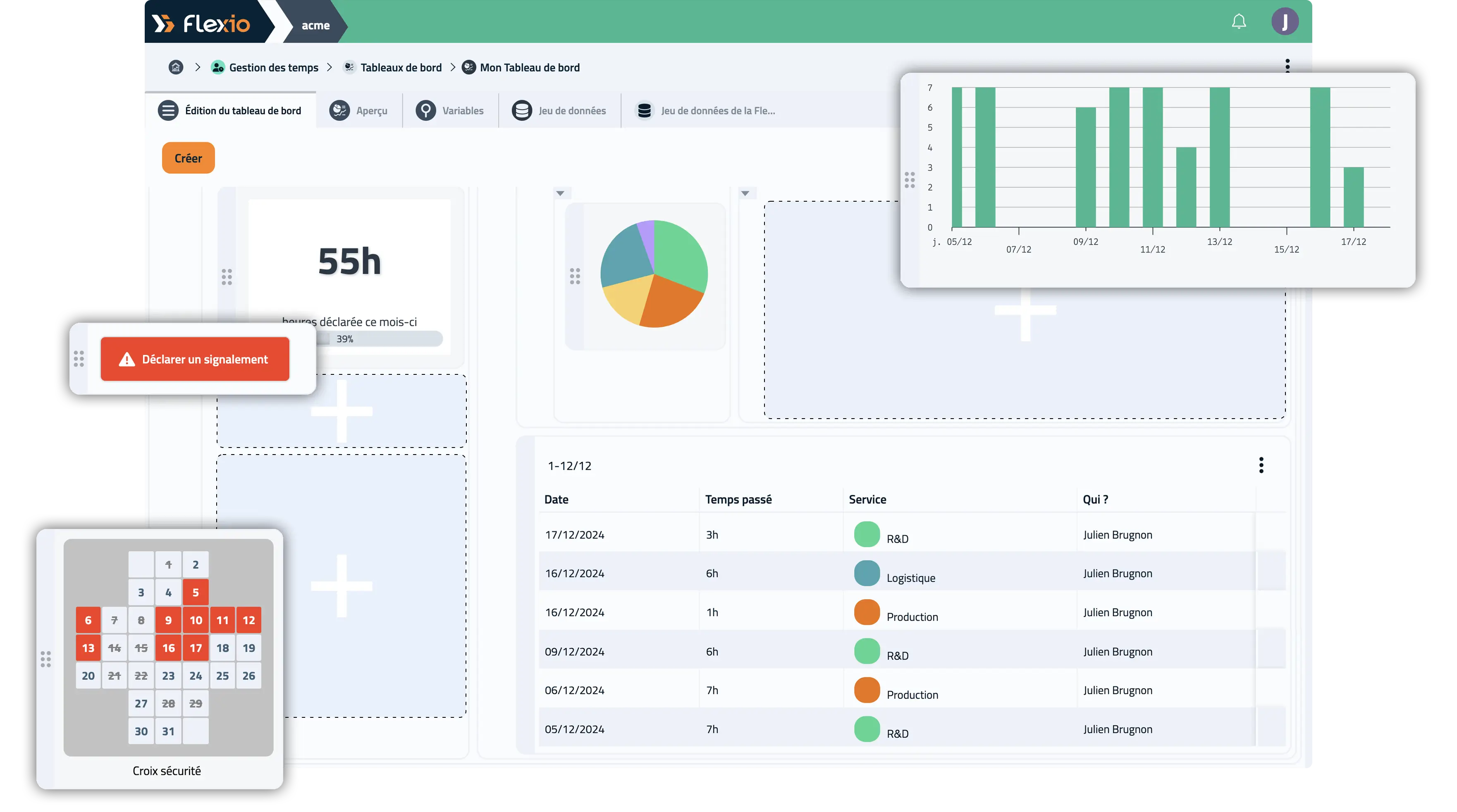
2. L'industrie 4.0 : accélérateur de l'amélioration continue
La transformation numérique révolutionne les méthodes traditionnelles d'amélioration continue. Les technologies de l'industrie 4.0 permettent d'amplifier les résultats et d'accélérer les cycles d'amélioration.
2.1 Les technologies clés au service de l'amélioration continue
La collecte de données en temps réel
- Capteurs IoT pour le suivi des équipements
- Applications mobiles pour les remontées terrain
- Formulaires digitaux remplaçant le papier
- Automatisation de la collecte des indicateurs
L'analyse prédictive
- Anticipation des dysfonctionnements
- Identification précoce des dérives
- Optimisation préventive des processus
- Aide à la décision basée sur les données
Le management visuel digital
- Tableaux de bord dynamiques
- Affichage en temps réel des KPIs
- Alertes automatiques sur écrans connectés
- Partage instantané des informations
2.2 Les bénéfices concrets de la digitalisation
Gain de temps et productivité
- Élimination des saisies manuelles
- Automatisation des tâches répétitives
- Accès immédiat aux informations
- Prise de décision accélérée
Meilleure traçabilité
- Historique automatique des données
- Suivi précis des actions correctives
- Documentation digitale des standards
- Capitalisation facilitée des bonnes pratiques
Collaboration renforcée
- Partage instantané d'informations
- Communication facilitée entre équipes
- Implication accrue des opérateurs
- Diffusion rapide des améliorations
2.3 Exemples d'applications dans l'industrie
Remontées terrain exhaustives et actions correctives suivies chez Cryostar (groupe Linde)
- Des remontées terrain facilitées et enrichies : les collaborateurs remontent les problèmes en quelques clics, photos et géolocalisation à l'appui. Un gain de temps et d'exhaustivité précieux.
- Une attribution des actions optimisée : grâce à des workflows intelligents, les signalements sont catégorisés et envoyés automatiquement aux bons interlocuteurs (maintenance, production, sécurité). Ceux-ci peuvent alors définir rapidement un plan d'action adapté.
- Un pilotage en temps réel de l'avancement : terminé les fichiers Excel et les reporting laborieux. Les tableaux de bord Flexio offrent une vision consolidée des indicateurs clés : nombre de remontées, criticité, taux de résolution, actions en retard… De quoi suivre la démarche au plus près et d'alerter si besoin.
Découvrez le retour d'expérience détaillé par ici (PDF) et le webinar dédié par là.
+7,5 min gagnées par contrôle et 3000€/an d’économies chez SANDEN
- Un gain de temps de 7,5 minutes par rapport de patrouille
- Une meilleure réactivité sur les non-conformités grâce aux alertes en temps réel
- Une réduction des coûts de non-qualité estimée à 3000€ par an
- Une fiabilisation des données et une traçabilité renforcée
- Une amélioration des conditions de travail et de la montée en compétence des équipes
Découvrez le retour d'expérience détaillé par ici (PDF) et le webinar par là.
3. Comment mettre en œuvre une démarche d'amélioration continue digitalisée ?
La réussite d'une démarche d'amélioration continue digitalisée repose sur une approche méthodique et progressive. Voici comment structurer votre transformation pour garantir des résultats durables.
3.1 Préparer le terrain
Identifier les priorités
- Auditer les processus existants
- Repérer les irritants quotidiens
- Mesurer la performance actuelle
- Définir des objectifs SMART
Impliquer les équipes
- Communiquer sur la démarche
- Former aux méthodes d'amélioration
- Recueillir les suggestions terrain
- Identifier les ambassadeurs du changement
Choisir le bon périmètre pilote
- Sélectionner un processus critique
- Définir des indicateurs mesurables
- Fixer des objectifs atteignables
- Planifier les étapes clés
3.2 Déployer progressivement
Phase 1 : Digitaliser la collecte
- Remplacer les formulaires papier
- Créer des applications métier simples
- Former les utilisateurs
- Mesurer les premiers gains
Phase 2 : Automatiser l'analyse
- Mettre en place des tableaux de bord
- Configurer des alertes automatiques
- Identifier les tendances
- Faciliter la prise de décision
Phase 3 : Standardiser et étendre
- Capitaliser sur les bonnes pratiques
- Documenter les nouveaux standards
- Déployer sur d'autres périmètres
- Former les nouveaux utilisateurs
3.3 Pérenniser la démarche
Animer au quotidien
- Rituels d'amélioration continue
- Suivi des indicateurs clés
- Célébration des succès
- Accompagnement terrain
Mesurer les résultats
- Suivi des KPIs définis
- Calcul du ROI
- Analyse des retours utilisateurs
- Ajustement des objectifs
Faire évoluer les outils
- Enrichir les applications
- Ajouter des fonctionnalités
- Intégrer les retours terrain
- Optimiser les processus
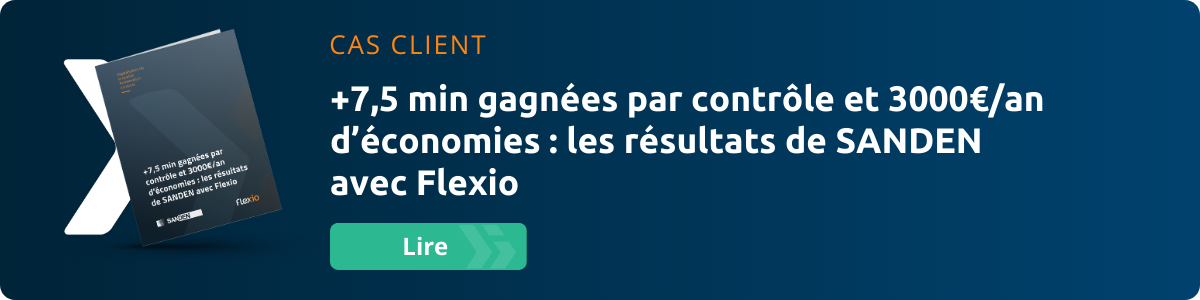
Conclusion : vers l'excellence opérationnelle digitale
L'amélioration continue reste plus que jamais un levier stratégique pour l'industrie. Si les méthodes traditionnelles comme le Lean et le Kaizen ont fait leurs preuves, leur association avec les technologies 4.0 ouvre de nouvelles perspectives d'optimisation. La clé du succès réside dans une approche progressive et pragmatique, centrée sur les besoins réels du terrain.
La digitalisation des processus d'amélioration continue permet de :
- Accélérer l'identification et la résolution des problèmes
- Impliquer plus efficacement les équipes terrain
- Mesurer précisément les gains réalisés
- Pérenniser les bonnes pratiques
L'enjeu n'est plus de choisir entre méthodes traditionnelles et outils digitaux, mais de les combiner intelligemment pour maximiser les résultats. C'est tout l'objectif de la méthode Flexio : permettre aux industriels de moderniser leurs pratiques d'amélioration continue, étape par étape, pour des gains rapides et durables.
FAQ : Les questions clés sur l'amélioration continue digitalisée
Comment démarrer une démarche d'amélioration continue digitalisée ? Commencez par identifier un processus critique mais circonscrit, avec des gains potentiels mesurables. Impliquez les équipes terrain dès le début pour co-construire les solutions. Flexio vous accompagne dans cette démarche progressive, de l'audit initial jusqu'au déploiement des premiers outils digitaux.
Quels sont les bénéfices concrets de la digitalisation des processus ? Les gains sont multiples et mesurables : réduction des temps de traitement (jusqu'à 60%), meilleure traçabilité des actions, réactivité accrue face aux problèmes, collaboration renforcée entre équipes. La digitalisation permet aussi d'automatiser les tâches sans valeur ajoutée pour se concentrer sur l'amélioration continue.
Combien de temps faut-il pour voir les premiers résultats ? Avec une approche progressive et bien structurée, les premiers gains sont visibles dès les premières semaines : économies de temps sur les audits, meilleure remontée des anomalies, suivi facilité des actions. L'important est de commencer par des "quick wins" pour démontrer rapidement la valeur ajoutée.
Comment garantir l'adoption par les équipes terrain ? La clé est d'impliquer les utilisateurs dès le début dans la conception des solutions. Les outils Flexio sont conçus pour être intuitifs et adaptés aux besoins réels du terrain. La formation et l'accompagnement continu garantissent une appropriation progressive et durable.
Quelle méthode d'amélioration continue privilégier ? Il n'y a pas de méthode unique. L'idéal est de combiner les principes éprouvés (Lean, Kaizen, PDCA) avec les outils digitaux adaptés à vos enjeux. Flexio vous aide à construire une approche sur-mesure, qui s'appuie sur vos forces existantes tout en modernisant vos pratiques.
Comment mesurer le ROI d'une démarche d'amélioration continue digitalisée ?Le ROI se mesure à plusieurs niveaux :
- Gains de temps sur les tâches opérationnelles
- Réduction des non-conformités et des coûts associés
- Amélioration de la productivité
- Augmentation de la satisfaction clientFlexio intègre des tableaux de bord permettant de suivre précisément ces indicateurs.