La réduction des temps d'arrêt est devenue un enjeu majeur pour optimiser la production industrielle et améliorer son efficacité. Dans un contexte où la transformation numérique bouleverse les modèles traditionnels, chaque minute d'arrêt machine impacte directement votre productivité. Les usines qui parviennent à maîtriser leurs temps d'arrêt gagnent un avantage concurrentiel décisif. Découvrez comment transformer cette problématique en opportunité d'amélioration pour votre site de production.
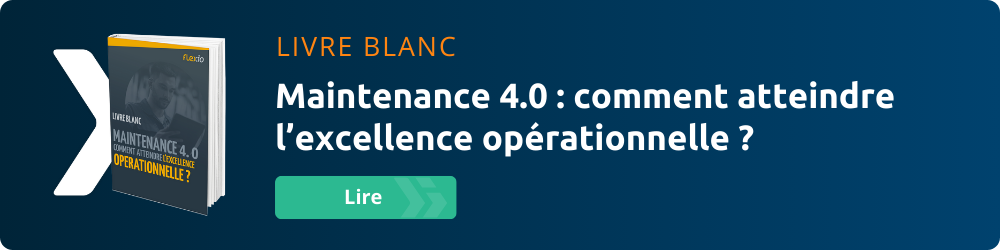
Définition et typologie des temps d'arrêts machine
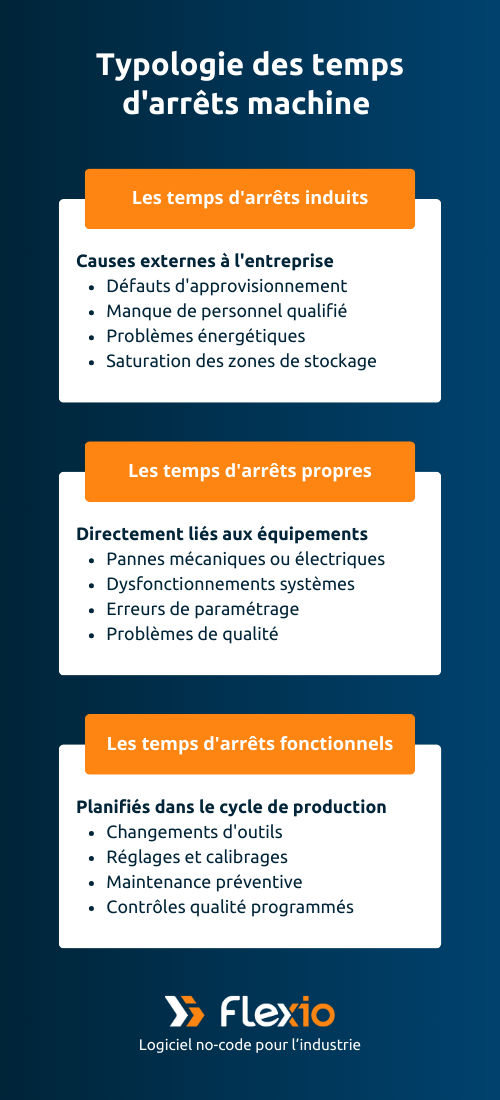
Les temps d'arrêts induits
- Causes externes à l'entreprise
- Défauts d'approvisionnement
- Manque de personnel qualifié
- Problèmes énergétiques
- Saturation des zones de stockage
Les temps d'arrêts propres
- Directement liés aux équipements
- Pannes mécaniques ou électriques
- Dysfonctionnements systèmes
- Erreurs de paramétrage
- Problèmes de qualité
Les temps d'arrêts fonctionnels
- Planifiés dans le cycle de production
- Changements d'outils
- Réglages et calibrages
- Maintenance préventive
- Contrôles qualité programmés
L'impact financier des temps d'arrêts : la réalité des chiffres
À première vue, il semblerait que les arrêts dit "urgents" affectent davantage les performances de la ligne de production et donc la productivité de votre usine. Ce type d'évènements mobilise une partie de votre équipe maintenance, qui doit chercher la cause de cet arrêt et remettre les équipements en état de marche le plus rapidement possible. Pendant ce temps, la productivité chute dans votre atelier, ce qui peut affecter l'efficacité et donc la rentabilité de votre usine.
Risques financiers d'un arrêt de production
Les arrêts de production dans l'industrie ont des conséquences coûteuses, principalement liées à la productivité. Un exemple frappant est l'industrie automobile, où une heure d'arrêt peut causer plus de 10 000 euros de pertes. Chaque usine peut calculer le coût horaire spécifique à ses équipements, en considérant l'impact sur la livraison, la facturation et le paiement.
Le coût des temps d'arrêt peut être mesuré en termes de pertes de production, de données, de réputation, ou même de vies. La méthode la plus répandue est de calculer la valeur financière de ces interruptions. Il est crucial de déterminer combien votre entreprise perd à chaque minute, heure ou jour d'indisponibilité de vos équipements.
Au delà du risque financier, l'impossibilité de livrer des produits finis, de qualité dans les délais, peut s'avérer problématique et engendrer une perte de confiance de la part des clients.
Les principaux effets d'un arrêt de production
- Ralentissement de la performance opérationnelle : micro-arrêts et baisses de cadence à répétition,
- Hausse des gaspillages, des non-conformités et des NVA (Non Valeurs Ajoutées) etc.
- Stress des opérateurs etc.
Pour autant, encore beaucoup de sociétés industrielles ne calculent pas les coûts relatifs à leurs temps d'arrêts. Autrement dit, peu d'entreprises s'appuient sur des indicateurs quantifiables et ont connaissance des coûts de tel ou tel dysfonctionnement. Cela, jusqu'à ce qu'elles subissent cette panne et qu'il soit trop tard.
4 stratégies efficaces pour réduire les temps d'arrêts machine
1. Modernisation de la maintenance industrielle : du préventif à l'intelligent
Objectifs : la modernisation de la maintenance vise à réduire les temps d'arrêt machine en anticipant les pannes. Cette approche de maintenance préventive permet d'optimiser la production tout en minimisant les arrêts non planifiés. L'objectif est de maintenir une production continue et efficace.
Étapes clés :
- Mise en place d'une maintenance préventive basée sur les données réelles
- Déploiement d'outils digitaux pour la documentation technique
- Installation de capteurs pour la surveillance des équipements
- Formation des équipes aux nouveaux outils digitaux
- Développement de la maintenance prédictive via l'intelligence artificielle
2. Exploitation des données en temps réel avec l'IoT industriel
Objectifs : l'IoT industriel permet une surveillance continue des équipements pour détecter les anomalies avant qu'elles ne causent des arrêts de production. Cette approche transforme les données machines en informations actionnables pour optimiser l'efficacité de la production.
Étapes clés :
- Identification des points de mesure critiques sur les équipements
- Installation des capteurs connectés aux points stratégiques
- Mise en place d'un système de collecte et d'analyse des données
- Configuration des alertes automatiques
- Création de tableaux de bord en temps réel
3. Formation et responsabilisation des opérateurs
Objectifs : la montée en compétence des opérateurs est essentielle pour réduire les temps d'arrêt machine. L'objectif est de créer une première ligne de défense capable de détecter et résoudre rapidement les problèmes, optimisant ainsi la production.
Étapes clés :
- Élaboration d'un programme de formation adapté aux nouvelles technologies
- Formation aux diagnostics de premier niveau
- Mise en place d'outils digitaux d'aide à la décision
- Création de procédures claires pour les interventions de base
- Développement d'un système de partage des bonnes pratiques
4. Optimisation de la planification de production
Objectifs : une planification optimisée permet de réduire les temps d'arrêt planifiés tout en minimisant leur impact sur la production. L'objectif est de synchroniser parfaitement les besoins de production avec les impératifs de maintenance.
Étapes clés :
- Analyse détaillée des cycles de production
- Synchronisation des interventions maintenance avec les arrêts planifiés
- Optimisation des changements de série
- Gestion prévisionnelle des stocks de pièces de rechange
- Mise en place d'un système de coordination production-maintenance
Les indicateurs clés pour piloter la réduction des temps d'arrêts
Les KPIs essentiels à surveiller
Le TRS (Taux de Rendement Synthétique) :
- Mesure globale combinant disponibilité, performance et qualité
- Indicateur de référence pour identifier les pertes de production
Les indicateurs critiques :
- MTBF : temps moyen entre deux arrêts machine
- MTTR : temps moyen de réparation
- Ratio préventif/correctif
- Taux de disponibilité des équipements
Un tableau de bord efficace pour optimiser la production
Visualisation et analyse :
- Affichage en temps réel avec alertes automatiques
- Suivi des tendances pour anticiper les dérives
- Rapports automatisés personnalisables
Actions d'amélioration :
- Identification rapide des causes d'arrêt
- Priorisation des actions correctives
- Suivi des résultats
Retour d'expérience client : DIEHL
Découvrez le retour d'expérience de notre client DIEHL dans le webinar dédié :
Le défi
Diehl, entreprise industrielle basée à Besançon et spécialisée dans l'usinage des métaux, cherchait à optimiser son processus de dégraissage des pièces. Suite à l'investissement dans une nouvelle machine de dégraissage, l'entreprise souhaitait digitaliser l'ensemble du processus pour :
- Réduire les temps d'arrêt machine
- Mettre en place une maintenance prédictive efficace
- Supprimer la gestion papier chronophage
La solution mise en place
L'équipe a développé une application sur mesure avec Flexio pour assurer :
- Le suivi proactif de la machine de dégraissage
- L'automatisation des processus d'homologation
- La centralisation des données de production
- La maintenance préventive intelligente
Les résultats obtenus
La transformation a permis des gains significatifs :
- Réduction du temps d'homologation de 3-4 semaines à moins d'une journée
- Suivi en temps réel des paramètres machines
- Traçabilité complète du processus de dégraissage
- Maintenance optimisée grâce aux alertes automatiques
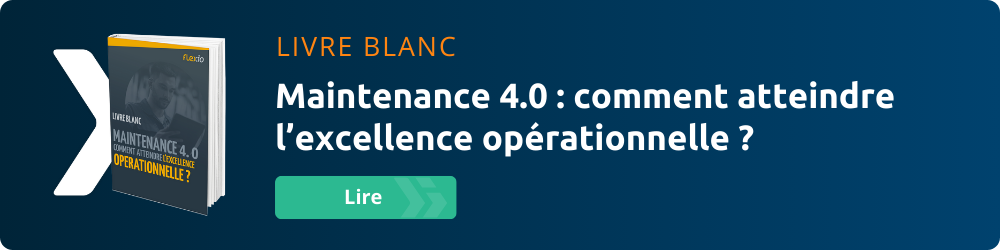
FAQ : vos questions sur la réduction des temps d'arrêt
Comment calculer le temps d'arrêt d'une machine ?
Pour calculer précisément le temps d'arrêt d'une machine, suivez cette formule :
- Temps d'arrêt = Temps total disponible - Temps de production effectif
- Incluez tous les types d'arrêts : planifiés, non planifiés, et micro-arrêts
- Utilisez des outils de suivi automatisé pour plus de précision
Qu'est-ce que la réduction des temps d'arrêt ?
La réduction des temps d'arrêt consiste à minimiser toutes les périodes d'inactivité des équipements de production. Elle englobe :
- L'optimisation des arrêts planifiés
- La prévention des pannes
- La réduction des temps de changement de série
- L'amélioration des processus de maintenance
Comment optimiser le processus de production ?
L'optimisation du processus de production passe par plusieurs actions :
- Mise en place d'une maintenance préventive efficace
- Utilisation de l'IoT pour le suivi en temps réel
- Formation continue des opérateurs
- Planification intelligente de la production
- Analyse régulière des indicateurs de performance